When installed, zinc roofing costs around $11.5 to $13 per square foot including labor and materials. For an average size 1,600 sq. ft. ranch or cape style zinc roof, your cost will be $18,400 – 20,800
Your total roof installation cost will vary depending on whether the previous roof will have to be torn off or not. Zinc roofing ranges in pricing depending on the region you live in and the availability of the material and installers who work with zinc.
If you are ready to replace your old roof, contact your local metal roofing pros for a FREE ESTIMATE.
Cost of Zinc Shingles and Standing Seam Metal Panels
Zinc metal shingles cost between $5 and $8 per square foot, and zinc standing seam panels cost around $6 to $10 per square foot.
Installing a metal roof is a more complex and time consuming process than installing asphalt shingles, which makes the professional cost to install a metal roof about 25% higher compared to the cost of installing shingles.
On average, metal roofing pros charge $4-7 per square foot for installation, depending on the type of metal roof you want, complexity of the job as well as local labor rates.
Installing a standing seam metal panels is more expensive than installing metal roofing shingles, so go for the latter if you are trying to cut down on costs.
You can use our Metal Roofing Calculator to estimate the cost of installing a zinc roof on your home.
Cost of Zinc Roofing vs Other Metal Roofing Materials
Per square foot, zinc costs $12 to $18 when installed. Copper is the most expensive metal roofing, costing over $20 per square foot.
Depending on the system, steel can cost from $7 to $12 per square foot, and aluminum similarly costs between $7.50 and $12.50 per square foot.
Factors That Increase Metal Roof Installation Costs
When budgeting for a new metal roof, there are a number of factors that you should keep in mind which may drive up the total cost of your new roof. You should discuss these with your contractor a head of time so that there are no financial surprises when roof replacement work begins.
– size of your roof
– roof slope (steeper roofs are more expensive). You can Estimate Roof Pitch
– metal roof type (metal shingles vs standing seam)
– number of floors in your house
– roof complexity and accessibility
– number of chimneys, dormers, valleys (each requires flashing work, and costs extra)
– tear off of the old roofing material. This can cost $1,000+
– type and quality of ventilation, underlayment and roofing accessories being used
– any damage to the roof substrate that needs to be repaired which can cost up to $600-800
Unique Beauty and Appeal of a Zinc Roof
Zinc’s unique physical properties give a zinc roof a sophisticated, striking aesthetic appeal. Unlike steel, zinc does not rust or corrode.
When zinc comes into contact with the carbon dioxide and moisture in the air, rather than rusting it develops a protective layer of zinc carbonate. The zinc carbonate patina has an attractive blue-silver tone that adds beauty to any building.
Zinc is also a versatile material that can be used in all sorts of roofing projects. It is a soft, pliable metal that can be worked into all sorts of designs. Because of this zinc can be used for unique architectural designs and more creative roofing projects.
It is also important to note that when installing a zinc roof in temperatures under 50 degrees Fahrenheit the material becomes brittle and may break, so hold off forming, trimming, breaking, or installing zinc roofing for warmer weather.
What Is Zinc?
Zinc has been used by European architects for hundreds of years because of its durability. It was also a popular roofing material in America, until it fell out of favor with the development of cheaper, shorter lasting materials such as asphalt. Now, homeowners and builders are looking towards zinc as an environmentally friendly, long-lasting roofing material.
Zinc is a naturally occurring metal, and is non-ferrous, meaning it does not contain iron. Zinc does not rust or corrode and takes very little energy to manufacture. It is also a very low-maintenance roofing material as it has self-healing capabilities.
Zinc is now a first choice roofing material for high-end new construction, upscale remodels, and historical renovations.
Will A Zinc Roof Corrode?
Zinc roofing does not corrode because of the zinc carbonate patina that forms on zinc roofing. Other materials, such as steel roofing, rust because of the oxygen content in the air, which leads to corrosion.
Zinc, on the other hand, self-generates a protective layer of zinc carbonate that prevents it from rusting and corroding.
What is Galvanic Corrosion?
Galvanic corrosion is caused by a reaction between two dissimilar metals, leading to corrosion. When two metals have a high electric potential between them, when they come in contact with water corrosion can occur. The larger the electric potential between the metals, the more severe the galvanic reaction will be, leading to more corrosion.
Bare zinc has a high galvanic reaction when placed by copper and non-galvanized or unprotected iron. This means that to prevent galvanic corrosion from occurring, zinc roofing should not touch these materials or even be in a location that will receive rain runoff that has been in contact with these metals.
Rain water runoff carries electrically charged ions from the dissimilar metals which leads to corrosion when in contact with zinc.
Zinc has a low galvanic reaction with metals such as aluminum and galvanized steel, so it can be placed near these materials with very low risk of galvanic corrosion. If copper or non-galvanized metal is unavoidable, there is a solution: coating zinc roofing with plastisol will protect the material from galvanic corrosion.
How Long Will a Zinc Roof Last?
Zinc roofing is known for its longevity. Because of its unique self-healing properties and protective zinc carbonate patina, zinc roofs last on average 80 or even a hundred years. That’s why zinc is a top roofing choice for historical buildings hoping to last for generations to come.
Durability of Zinc Roofing
Because of its unique characteristics, zinc is a particularly durable material for roofing. While scratches on other metals such as steel can lead to rusting and corrosion from oxidation, zinc’s patina prevents this from happening.
The layer of zinc carbonate that forms on zinc roofs regenerates over time, healing all scratches on the surface of the roof. It also prevents zinc roofs from experiencing corrosion. This self-healing property is what makes zinc such a durable material.
In addition to these properties unique to zinc, this roof offers excellent protection that only metal can give you. A zinc metal roof will protect your home pretty much against any weather conditions, including extreme weather, such as:
– hurricane level wind
– snow storms
– ice dams
– rain storms and any type of water leaks
– damage from extreme heat and sun’s UV rays
– fire
– hail and any other type of major impact
– Rot, insects, fungus, etc
– There will be no warping, splitting, chipping, cracking, etc as common with other types of roofs.
Essentially, a zinc roof will offer you complete peace of mind in any region of the country and in any weather.
Conditions That Prevent a Zinc Roof From Forming a Protective Patina
Since the zinc carbonate patina is so critical to the durability of zinc roofs, it is very important to consider the instances in which the roof does not form this protective layer. Carbon dioxide and moisture makes zinc form the patina.
However, if moisture is present but carbon dioxide is not—think backsides or undersides of zinc panels that are not exposed to air—white rust can form. This rust will continuously deteriorate the zinc and can cause damage to the roofing.
To mitigate this, any area exposed to moisture but not carbon dioxide should be coated. Interior sides of gutters, undersides or backsides of wall panels or standing seam roof panels, should always be coated to prevent white rust. Good ventilation that moves the moisture away from the roofing can also help prevent white rust from forming.
Is Zinc Roofing a Green Building material?
Zinc is an excellent material choice for the environmentally conscious. For one, zinc is completely recyclable and can be reused, from building scraps until the roof reaches the end of its lifetime. Asphalt roofing, on the other hand, produces tons of waste and fills landfills.
Zinc is a fungistat, which means it prevents the growth of fungus, mold, and mildew. While that helps the cleanliness and maintenance of the roofing, it also helps the environment. When water runs off from other metal roofing materials that are fungicides (kill fungus) like copper, it can kill vegetation in addition to killing the fungus.
Water runoff from zinc roofs, on the other hand, just prevents fungus from growing and does not harm vegetation. Also, the water runoff from zinc roofs is considered clean, making it a great roof choice for those interested in rainwater collection.
This is why you can use zinc roofing strips on an asphalt roof to prevent ugly black streaks.
Zinc also takes less fuel to manufacture, shape, and produce it, helping cut back on fuel emissions. It also reflects solar heat, helping keep cooling costs low in the summer and cutting back on emissions.
Green Eurostyle Zinc Gutters
Zinc is known for its environmentally friendly rainwater drainage. Because zinc is a fungistat metal, the runoff from the zinc roof does not harm any foliage beneath it. The water that drains from the roof during rainfall is considered clean and safe to drink (if there are no other mitigating factors like smog).
To match the long-term lifetime of zinc roofs, the “European Style” zinc drainage gutter system is the best fit because it is designed to withstand the stress of decades of water drainage. The European style zinc drainage system has several unique features that make it well-suited for zinc roofs.
First of all, the European style drainage system has half-round gutters which have a deeper profile than the alternative “American Style” drainage system. The European style gutters also come with a back lip that prevents the water from overflowing and also locks the gutter into place when there are overlapping sections.
The downspouts in European style drainage also add to the durability of the system. The systems employ long lasting seamless-weld downspouts and a custom fit flared end that prevents water from leaking. Roof drainage components and accessories must also be high quality in the European drainage system, such as hangers, brackets and elbows, and miters.
In contrast to zinc rainwater drainage systems like the European system, other common gutter systems like those made from aluminum have many downsides.
For one, aluminum drainage systems must be replaced every fifteen to twenty five years. This means that an aluminum drainage system would need to be replaced between four and seven times before a zinc drainage system needs a single replacing.
Like zinc roofing, the zinc European drainage system has a higher upfront cost but pays off in the long run. The drainage system is long lasting and environmentally friendly, and combined with the environmental benefits of a zinc roof the water drainage system can truly be considered ‘green’.
Thermal Expansion and Contraction Considerations for a Standing Seam Zinc Roof
It is very important to consider the expansion and contraction of zinc roofs. All metals expand and contract based on temperature changes, but zinc experiences particularly large changes.
When exposed to a temperature differential of 160 degrees Fahrenheit, common throughout the United States, zinc can expand up to an inch for every thirty feet of standing seam. This is twice as much as steel.
Zinc roofs must be built to allow for thermal movement. Panels cannot be restricted by clips or fasteners, or else they can billow and buckle from thermal expansion.
If the panels do not have the necessary space to move, the water-tight sealant can become less effective. Trim should be given a quarter inch space at end laps to allow for thermal movement.
This is why its so important to hire a highly experienced professional metal roofing installer who knows all the nuances of proper installation, so that your zinc roof will not have any issues down the line. Its too expensive of an investment into your home, to try to save a few bucks on high-quality labor.
Areas and Locations to AVOID installing a Zinc roof
Zinc roofing should not be installed in areas near salt-water oceans that experience low rainfall levels, because the salt can damage the zinc if it is not washed away by rain.
Zinc should also not be in contact with acidic woods such as oak, birch, or cedar without a plastisol protective coating. Less acidic trees like pine, spruce, and poplar can be in direct contact with zinc roofing.
Additionally, a zinc roof should also not be in contact with concrete or bituminous felt without the proper coating. This is because concrete and bituminous felt hold moisture, so in areas without carbon dioxide present, white rust can form on the zinc. Good ventilation can also keep the moisture away from the zinc.
Zinc vs Asphalt Shingles
Zinc roofs have around five times the lifetime of asphalt shingle roofs that need to be replaced every ten years. Zinc is also more energy efficient than asphalt, because it reflects off solar heat and prevents heat accumulation in attics.
Research by the Florida Solar Energy Center found that metal roofs can save up to 20 percent on energy bills because they absorb 34 percent less heat than asphalt shingles.
Zinc Roof vs Premium Roofing Materials
Zinc has many attractive qualities compared to other premium roofing materials options. For instance, while copper shares many features of zinc roofs, it is twice the cost. Unlike copper roofs, Zinc’s water run-off from rain is clear and will not stain nearby materials.
Cheaper metals used on roofing, on the other hand, like painted aluminum, or corrugated metal panels can scratch or rust easily if not properly protected. Zinc’s protective coating and self-healing properties keep it good as new.
Real slate and clay tile are much heavier than zinc, so they can only be used on buildings with stronger (and more costly) structural bases.
Zinc Roofing for Historic Homes
Zinc is an excellent choice for historic homes. In the 1800’s, zinc roofs were a popular choice in France, Germany, and Belgium, and many of them can still be seen today. In America, many early builders and designers—including Thomas Jefferson—saw the value in zinc roofing.
Here’s what makes zinc such a good choice for historic homes:
● Zinc is long-lasting, a perfect fit for historic buildings hoping to last for generations to come.
● Zinc’s low maintenance nature makes it a good fit for historic renovations that have well-funded budgets for initial costs but not for regular upkeep, because zinc requires little maintenance.
● Zinc’s color is similar to traditional turn-coated lead roofs, lending aesthetic authenticity and ensuring that the new roof aligns with the historic image of the building
Summary of Zinc Roofing’s Advantages
Zinc has many important advantages. For one, while the initial payment may be higher than asphalt roofing or other metals, it is cost effective in the long-run because of its hundred-year lifetime and superior weather protection.
The protective zinc carbonate patina has many advantages, including self-healing and the prevention of rust and corrosion. Zinc is also fire resistant and insect resistant, making it a good choice for areas prone to fires and insect infestations.
Zinc also is energy efficient because it reflects off sunlight and prevents heat from accumulating, helping buildings stay cool in the summer.
Moreover, zinc is rightfully considered one of the most beautiful roofing materials, the likes of which cannot really be replicated by man-made technology.
Zinc roofing begins as a dark gray color, and as the patina process begins the roof develops a bluish or light gray color. As the patina continuously regenerates, the color always looks crisp and scratches and other marks disappear.
Zinc is an all-around excellent roofing material choice for those looking for a long-lasting, weather-proof and eco-friendly option.
Disadvantages of a Zinc Roof
Zinc roofing does have some disadvantages.
First, the upfront cost to zinc roofing is the second-highest in the industry, up to $20 per square foot when installed.
Copper roofing is the only other roofing material more pricey than zinc.
However, zinc will outlast almost any other option, requiring minimal maintenance, making the investment worthwhile in the long run, especially if you plan on remaining in the home for a long time.
Another potentially negative aspect to consider is the variability of the protective zinc carbonate patina. While for some buildings the patina can form in two years, sometimes it can take up to thirty years.
This variability depends on the climate: the patina forms faster in warmer, more humid climates. Without the patina, the zinc roof can lose many of the attractive features that draw people to zinc roofs, like the self-healing quality and the prevention of corrosion and rust. The patina may also not form uniformly, and the color may differ across the zinc roof.
Zinc roofing can also run into problems when not installed properly. For instance, if non-breathable synthetic underlayment is used, moisture can be trapped between the roof and the roofing deck.
Also, if the panel backsides are exposed to water, they can corrode. To prevent these issues, make sure to hire a trusted professional with experience installing zinc roofs.
Is a Zinc Roof Worth It?
Zinc roofs have an excellent Return on Investment (ROI), making them a good choice if you are thinking of selling your zinc-roofed building down the road.
Metal roofs in general have good ROIs, with a recoup value of around 86%. On the East coast of the United States, metal roofs have an even higher ROI of 95%.
There isn’t exact data on the ROI of zinc roofs compared to other metal roofs, but the ROI may be even higher because of its highly attractive qualities.
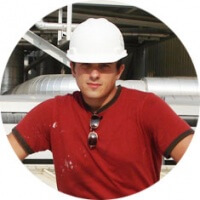
For over 20 years Leo has run a successful roofing business in New England, specializing in metal roofing, as well as cool flat roofing technologies. Having replaced and installed hundreds of roofs in New England, Leo has first hand experience with pretty much every residential roofing material and roofing manufacturer available in the US.