Membrane roofing is a commercial standard that can also fit many residential homes with flat or low slope roofs. There’s a wide range of membrane roof options from reputable brands like Firestone Building Products, Carlisle SynTec Systems, and GAF.
Typically membrane roofs are made from such materials as: EPDM, TPO, and PVC, ranging in price from $5 to $12 per square foot.
One consideration to remember is the membrane roofs’ installation complexity, as some methods require special equipment or exceptionally skilled labor.
Luckily, it’s worth it, as a membrane roof has numerous advantages, including durability, energy efficiency, and flexibility. With proper installation, a membrane roof can provide long-lasting protection and aesthetic appeal for your building, all within a reasonable budget.
What Is A Roofing Membrane?
Keeping moisture out and protecting the interior of a low or flat-roofed structure requires a membrane, which is a thin layer of waterproof material that acts like a shield from the elements.
These roofing membranes can be crafted from various materials – rubber, plastic, modified bitumen – all reinforced for strength and durability to keep water at bay.
Even in the harshest climates, these roof membranes can withstand weather conditions and provide long-lasting protection for the home beneath.
Average Total Cost of a Membrane Roof
Replacing a membrane roof can be relatively expensive, with the average cost being $7.25 per square foot.
Many homeowners pay from $6.50 to $8 per square foot for the project. That’s an increase of about 25 cents more than in 2019, and it doesn’t look like prices will go down until at least 2024.
There’s plenty to consider when estimating roof replacement cost: roof size, the type of membrane, the installation process, and how well-kept the existing roof is all play into the final price tag you’ll get.
Moreover, it’s easy for these costs to add up quickly if you don’t budget properly.
You can use our Flat Roof Cost Calculator to estimate the cost of replacing your flat roof.
Roof Membrane Cost by Material Type
Each type of roof membrane will slightly differ in cost from the others. Let’s take a closer look at several types of roof membranes and their prices.
Membrane Roofing | ||
---|---|---|
Roof Membrane Type | Price per Square Foot | Total Cost for 2,000 Square Feet |
SBS Modified Bituminous | $3-$4 | $6,000-$8,000 |
APP Modified Bituminous | $3.50-$5 | $7,000-$10,000 |
Built-Up Roof Membranes | $5-$7 | $10,000-$14,000 |
EPDM | $4-$6 | $8,000-$12,000 |
TPO | $5-$7 | $10,000-$14,000 |
PVC | $6-$9 | $12,000-$18,000 |
KEE | $6-$10 | $12,000-$20,000 |
Elastomeric/SPF | $4-$6 | $8,000-$12,000 |
Liquid | $3-$5 | $6,000-$10,000 |
SBS Modified Bituminous Roofing
The Styrene-Butadiene-Styrene (SBS) Modified Bituminous roofing is a great pick for commercial buildings.
At around $3 to $4 per square foot for materials, with labor costing an additional $3 to $4, this roofing type can be economical, which is desirable when covering a large building. What really stands out is its flexibility and resilience amidst extreme temperature changes.
Using the SBS modifier gives the material rubber-like properties that make it resistant to cracking or splitting even with drastic shifts in weather.
This roofing is best for regions with variable climates and can be installed through hot asphalt or cold adhesive methods.
Did you know? The membrane roof has been common in commercial and industrial buildings for a long time. But flat roofs and, thus, membranes have gotten increased attention in the residential realm thanks to their energy efficiency and waterproofing. Those with modern, recently-constructed houses who want to reduce energy costs might consider membrane roofing.
APP Modified Bituminous Roofs
Atactic Polypropylene (APP) Modified Bituminous roofing is an upgrade in the roofing world.
Although more costly at $3.50 to $5 per square foot for materials and labor, APP provides superior rigidity and heat resistance than other types—ideal for warmer climates.
It’s also applied using a torch method which speeds up installation but is riskier and demands experienced professionals.
APP isn’t just known for durability. It’s also quite easy on the eyes, making it perfect when you want appealing aesthetics and quality performance.
Built-Up Roof Membranes (BUR)
The Built-Up Roof (BUR) membrane gives reliable roofing with superior waterproofing and an extended lifespan. Suited for nearly any roof, BUR is a multi-layered solution with alternating layers of bitumen and reinforced fabric.
The BUR system is an excellent value at $5 to $7 per square foot, including materials and labor. And for additional protection against the elements, coat the surface with gravel or use an energy-efficient reflective coating.
EPDM Rubber Roofing Membrane
Ethylene Propylene Diene Monomer (EPDM) is one of the most cost-effective roofing membranes you can use to replace your flat or low-sloped roof.
A synthetic rubber membrane with remarkable elasticity and weather resistance, EPDM roofs come in at around $4 to $6 per square foot and stay strong for years with the right care.
Roofers can install these lightweight EPDM rubber roof membranes using several methods, including fully adhered or mechanically fastened.
Most significantly, all that flexibility offers greater protection against harmful UV rays. With a little care and attention, this roofing material will last you a good long while.
TPO Roofing Membrane
TPO roofing can also offer great value for the money you put into it, with prices ranging from $5 to $7 per square foot.
By installing TPO on your rooftop, you are choosing a highly efficient option due to its reflective white surface that bounces back the sun’s heat which in turn reduces cooling costs.
TPO roofs are also resistant to UV rays, chemicals, and punctures.
All these features make it a material that commercial building owners widely favor. The seams of the membrane can be heat-welded together, providing ultimate strength and preventing water from seeping in.
Pro Tip: When thinking about membrane roofing installation, consult a professional contractor specializing in this type of installation. They can assess your roof, consider your expectations, and recommend the best material and installation method for the climate and building structure.
PVC Roofing
Polyvinyl Chloride (PVC) roofing costs $6 to $9 per square foot, all with materials and installation. It’s a common material in industrial settings due to its strong, flexible structure that can resist harsh chemicals and heat.
But it’s not just durable and watertight; the seams are heat-welded for an extra layer of protection from the elements.
So if you need a material that guarantees a tight seal, especially if you live in an area with higher pollution levels, PVC could be good for you.
KEE Roofing Membrane
Ketone Ethylene Ester (KEE) roofing is not the most price-friendly one, but still affordable, with installation estimates ranging from $6 to $10 per square foot.
This top-notch material offers tremendous protection against harsh chemicals, UV rays, and punctures, making it ideal for locations where durability matters most.
A KEE roof will provide reliable shelter year after year while requiring very little upkeep.
Elastomeric/SPF Membrane
Installing roofs with Elastomeric or Spray Polyurethane Foam (SPF) could cost you somewhere between $4 to $6 per square foot, including materials and labor.
SPF is a foam-like material applied by spraying and expands to form a uniform layer consistent with the roof’s shape.
It’s an exceptional insulator for a house or commercial building and adds a bit of shine to its look. The elastomeric coating shields the roof from UV light, thus preserving its appearance.
Liquid Roofing Membrane
Liquid-applied roofing has been gaining popularity, as its flexibility leads to various creative benefits.
It forms a seamless waterproof seal and is incredibly convenient for roofs with complex shapes.
The cost is mid-range compared to other roofing materials—averaging around $3-$5 per square foot with installation included.
The “ease of maintenance” factor and its design flexibility make this roofing type well worth the money. Better yet, you can even customize the roof with various colors and finishes.
Did you know? Some membrane roofing materials use environmentally friendly practices in the manufacturing process. That may be recycled content or materials that can be recycled at the end of their lifespan. If sustainability is important to you, be sure to ask about these options.
Additional Cost Factors To Install A Roofing Membrane
Material prices and contractor rates are the biggest contributors to the price of roofing, but there are other factors that will affect the final cost.
Here’s a detailed look at these factors to remember when budgeting:
The roof’s dimensions will define its overall cost, not only due to materials. The larger it is, the more time and resources it takes to complete the install.
High-end materials like Polyvinyl Chloride (PVC) and butyl rubber materials (KEE) can be quite pricey compared to the more affordable Ethylene Propylene Diene Monomer (EPDM). Thus, your choice of membrane should depend on your budget.
More complex installation methods will cost you more. As an example, a torch application may call for a higher-skilled contractor, while a fully attached roofing could take more sealants and adhesives.
If your roof has many , such as chimneys, vents, and skylights, the installation can be tricky. It will take extra effort and materials to guarantee a tight seal.
Moreover, the roof’s existing condition can drive the cost of repairs. If there’s underlying damage, it might take extra effort and materials to ready the surface for application.
Lastly, depending on which roofing material is currently in place and how stringent local disposal regulations are, taking it down and disposing of it could set you back an extra $1 to $4 per square foot. The price includes manual labor for uninstalling it, fees for dumping debris, and potential charges for recycling materials.
The geographical location and contractors’ capacity to access the rooftop can significantly impact the final cost of installation. Remote access or hard-to-reach spots might require additional equipment, while the local charges for services and products could differ depending on the area.
Extended warranties and regular maintenance packages can also add to the initial cost you’ll need to budget. However, they can save money in the long run by extending the roof’s lifespan.
Top Membrane Roofing Manufacturers
Manufacturers of membrane roofing will dictate the quality and variety of products you’ll find on the market. Here’s an overview of some prominent membrane roofing companies:
Firestone Building Products have an impressive line of products that are sustainable, resilient, and energy efficient. Their EPDM and TPO membranes are particularly renowned for surviving in extreme weather conditions.
Carlisle SynTec Systems are one of the industry experts in single-ply roofing. Their cutting-edge FleeceBACK membranes are excellent anti-puncture protectors that last many decades.
As a leading roofing manufacturer in North America, GAF has a broad selection of membrane roofs, such as TPO and PVC, to fit both residential and commercial customers.
They also offer traditional shingle roofs that give a home a warm, snug feeling, along with extensive flat roofs for businesses.
Johns Manville is one of the go-to providers for environmentally conscious roofing membranes. Their full suite of products includes EPDM, TPO, PVC, and more, along with insulation and cover board. Roofing materials can impact the environment more than one might assume, so it’s worth being green.
Sika Sarnafil is a major manufacturer of PVC roofing membranes in particular. These durable and quality roofing products stand up to any elements with design flexibility that allows for creative expression. They have a reputation for appealing aesthetics and superior weather protection.
This list of manufacturers is by no means final. You can find many specialized products that would benefit you in energy efficiency, aesthetic appeal, and unique installation requirements.
Conduct thorough research and consult with roofing professionals to make the right decision for you and your house or commercial building. They will understand your needs best and can direct you to a manufacturer or specific product that does exactly what you’re looking for in membrane roofing.
Pro Tip: Installing a flat roof is pricey, time-consuming, and complex. Therefore, you want your roofing to last as long as its construction permits.
Inspect it frequently and maintain it well to give it the best chance. Check for signs of wear, damage, or leaks and address them promptly if you find any. Consider setting up a routine schedule with a roofing company to check it up professionally.
What Are the Advantages of a Membrane Roof?
The many advantages of membrane roofing make it appealing to many building owners. Its construction is robust, so it’s resilient in the face of harsh weather conditions.
As such, external forces have a lesser impact on its life expectancy than some other roof types. Many membrane materials possess reflective properties that shield against harsh and potentially harmful UV rays and reduce energy consumption.
A membrane roof is also quite flexible, giving architects the freedom to customize the roof for various shapes and sizes. Installing membrane roofing can take less labor and be faster compared to traditional methods (depending on the type).
Its seamless nature waterproofs the roof better than shingles and protects the building from leaks and water damage.
Last but not least, a few membrane materials are recyclable or contain recycled content, thus making them ideal for those wishing to pursue eco-friendly practices.
Does a Roof Need a Membrane?
If you have a low-sloped or flat roof, then you also need a membrane. The membrane will act as a defensive shield from the elements and keep your roof in good shape and safe from external harm.
It’s seamless, so it guards against water infiltration and also helps keep energy costs down by acting as an insulator.
The extra layer of protection will extend the roof’s life expectancy, which is great if you want to invest once and not worry about it for decades after.
How Long Should a Membrane Roof Last?
The life of a membrane roof varies, with an expectancy anywhere between two to three decades, but it can last much longer than that.
Several factors can impact these estimated timelines, including the composition and quality of the material, how well the installers take care of it, proper routine maintenance, and the local environment and climate.
Can You Double-Layer Membrane Roofing?
You can reinforce a building with two layers of membrane roofing but with a caveat. This technique can potentially add an extra layer of insulation and make the roof more durable long-term.
Yet, it must be carefully done while paying close attention to the building plan. The building must carry the weight properly to avoid structural issues or the threat of collapse.
Did you know? Membrane roofing has more to offer than practicality. The many colors, patterns, and textures on the market let you create a unique roof that complements your property’s aesthetics.
You don’t have to settle for conventional shingles or tiles, even if you like their looks. Some membrane materials imitate these elements so closely it’s hard to tell the difference.
Are Membrane Roofs Any Good?
Membrane roofs can be terrific if they match what you seek. The integrity and strength of membrane roofs have made them sought-after in the construction industry.
These durable, lightweight structures are lauded for versatility, cost-effectiveness, and reliable performance, whether for commercial or industrial use.
Membrane Roofing Is The Way To Go!
A membrane roof is robust and versatile, so it fits perfectly with modern flat roofing construction.
There’s a range of choices in materials, costs, and benefits.
With savvy material selection and high quality installation, this resilient roofing material can grace your home with years of protection from the elements and a spectrum of other benefits.
As time goes on, membrane roofing remains a prime example of engineering ingenuity with enduring resilience and building convenience that started as an uninspiring commercial solution and grew to be a modern marvel.
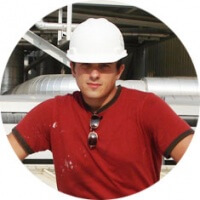
For over 20 years Leo has run a successful roofing business in New England, specializing in metal roofing, as well as cool flat roofing technologies. Having replaced and installed hundreds of roofs in New England, Leo has first hand experience with pretty much every residential roofing material and roofing manufacturer available in the US.