Flat roof insulation is one of the most important and misunderstood building components.
There are many different types and insulation installation methods out there, along with a lot misinformation about which insulation products offer the greatest energy savings.
Here, we share the most common mistakes people make when installing insulation on a flat roof
We will also offer our professional take on what insulation actually works, how much it costs and the benefits you get as a homeowner.
Average Flat Roof Cost:
Low End
$6815
|
Mid Range
$8769
|
High End
$11211
|
|
Flat Roof Insulation Materials To Avoid
Some so called “experts” online may recommend the following, claiming to achieve a greater r value at a lower cost.
Mistake # 1: Save money by installing Fiberglass Insulation, and framing out roof slope using OSB board substrate<>
When a homeowner really needs to cut down on costs, some contractors may suggest the following:
Add an additional layer of OSB over the sheathing. It should be installed on tapered 2x furring strips, in order to slope the surface of the roof toward drains. Then, install R-30 fiberglass batts between the rafters.
Our Take: Framing this out and buying 30-R fiberglass insulation will cost you about 50% more than just buying 5 inches of PolyISO (equivalent of 30-R).
Because it will take a lot of time to actually install all of this, you are risking major leaks, if it starts to rain before everything is complete. Also, if a roof leaks and fiberglass insulation gets wet, it will loose most of its insulating properties.
Moreover, you are also risking that underneath this wet insulation, you roof sheathing and deck will start to rot. The worst part about this: you will not even know its happening. These problems typically come out when its too late to fix the roof, and complete replacement is in order.
However, PolyISO absorbs considerably less water, therefore if it gets wet, it looses only a small fraction of its insulating properties. If moisture is a major concern, you can also install XPS rigid insulation, which offers superior moisture resistance.
While expensive, the best insulation is PolyISO rigid foam. It is top quality and the most cost effective product for your flat roof.
You can expect to pay about $55/100 sq. ft. for a 1 inch board (equivalent of 6 r value). We recommend having at least 20 r value worth of material for optimal energy efficiency.
Mistake # 2: Combining different types of insulation to increase R value
If someone wants to get a very high r value without breaking the bank, some contractors may propose this:
Install 4 in. of rigid foam on top of the deck, 2 in. of closed cell foam under it, as an air barrier. Then, R-30 batts can be added for additional efficiency at a lower price. This option can give you a total r value of about 62.
Our Take: The extra labor required to get inside a typically inaccessible crawl spaces under a flat roof will more than negate potential savings of using 30-R fiberglass batts.
If on top of this you have to hire a spray foam specialist to install only 2 inches of foam, your costs will skyrocket.
Once again, increasing the thickness of ISO will give you a higher r value at a much lower total cost. If you can actually get into the crawl space, its much more effective to install blown in cellulose or fiberglass insulation.
Mistake # 3: Yet another wrong way to raise the R value at a low cost
This error is similar to the one above. Some pros may suggest it to a homeowner looking for alternative insulation materials that are inexpensive.
First, install sloped decking as described in the first option. Then, do 2 in. of closed cell foam insulation and fill out the remaining 10 in. of the roof cavity with dense packed cellulose. With this combo, you can achieve a total r value of about 47.
Our Take: Framing out a new sloped roof while making sure that your old one does not leak during this process will cost about 50 % more than to add a quality PVC membrane and 6 inches of ISO or another high density rigid foam.
Mistake # 4: Using fiberboard
If you tell a roofer you are on a really tight budget, he may try to convince you to do the following:
Install fiberboard insulation, because it will save you hundreds of dollars.
This scenario often happens if you hire a cheap roofer, who typically installs EDPM rubber.
Our Take: This is a REALLY BAD idea! Fiberboard is not an insulation. It has only 1-r value per inch and is always installed in 0.5 inch thickness. Therefore, you get practically 0 r value out of it.
Additionally, attic condensation and leaks will make fiberboard wet. Moisture will be trapped inside, causing mold growth and further reducing its efficiency.
Fiberboard is intended as a glue-down surface on roofs above none-living spaces, such as garages or porches, where r value is not needed. Living spaces should have real insulation, and the more of it the better.
If your contractor suggests using fiberboard, we recommend that you fire him immediately. Clearly, he does not care about your roof or you, and will likely do a very sub-par job.
Why Its Important To Insulate Your Flat Roof
While insulation for a flat roof is expensive and can account for as much as 25% of the total installation cost, there are a number of important benefits to having it in place.
1. Reduce extreme temperature fluctuations inside your home
When you have an un-insulated roof, you have to live with rather uncomfortable room temperatures inside the home. During the cold months, warm air will quickly rise up and escape through the roof, leaving the rooms very chilly.
The opposite happens in the summer: hot air gets trapped inside, making the room unbearably hot and sticky This is particularly true on roofs that are dark and have a low insulation r value.
It is important to note that Polyiso has the best performance in warm climates. Its insulating properties are worse in extremely cold temperatures. If you live in a region that is cold for many months of the year, you should consult a professional on the best insulation type for your house.
2. Improve energy efficiency
A roof without good insulation is a great contributor to energy loss. This is bad for the environment and for your wallet, as you end up spending a lot more on your electric bills.
Proper insulation can significantly reduce your energy consumption (heat in the winter, AC in the summer) and reduce your energy costs by hundreds of dollars a year.
A high r value of 20 or more, combined with well insulated walls and energy efficient windows can reduce your heating and cooling expenses by as much 30% every year.
Therefore, it will pay for itself within 4-6 years in energy savings alone. If you have oil heat, the pay-off will be even faster, and you will be saving money for many years there after.
As you can see in the image above, the roof is not the only area in the house where energy loss occurs. Thus, for optimal savings, you want to ensure that your entire house has proper insulation, including walls, flooring, windows, etc.
However, a roof is a good place to start, since it is the second larger contributor to energy loss, after walls.
3. Prevent rotting of the sheathing and roof deck
Across the US, the majority of flat roofs either have no ventilation at all, or are poorly vented. This is due to faulty original architectural design that did not take proper venting into account.
As a result, if you open up most flat roofs, especially those located in places like Arizona, you will see a lot of moisture, rot and mold as a result.
This problem also occurs in roofs that have fiberglass batt insulation and no venting. Sometimes, inspectors find that it is completely wet; there is severe rot and mold growing in the sheathing.
To mitigate venting issues, and still have all the benefits insulation offers, its ideal to install high quality foam board products, such Polyiso or XPS. They are not susceptible to moisture infiltration and will keep the roof dry, even without a good ventilation system.
You just need to make sure that you put in enough insulation to keep the sheathing above dew point temperature in the cold months. For best protection, professional contractors recommend at least 6 inches of foam insulation board.
Cost per sq. ft.
Roof Size:
Roofing Material:
See costs in your area
Start Here - Enter Your Zip Code
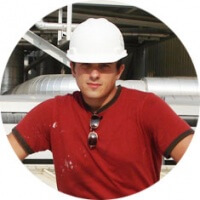
For over 20 years Leo has run a successful roofing business in New England, specializing in metal roofing, as well as cool flat roofing technologies. Having replaced and installed hundreds of roofs in New England, Leo has first hand experience with pretty much every residential roofing material and roofing manufacturer available in the US.
Can Rmax be installed under osb on a flat roof ? Thank you
I live in San Francisco, California, with a 1700 square foot flat roof, wanting to replace my old “tar & gravel” roof. As you may know, San Francisco typically has more cool and foggy days than “hot” days, so I am considering using a black (rather than white/light-colored) roofing material.
I received this quote, for $16,800 (Without Insulation); $8,000 (with Insulation) from a licensed, bonded, and insured local roofer.
PREPARATION:
1. Tear off existing roof layers (tar and gravel) to the original sheathing.
2. Only if needed, repair/replace damaged under sheathing for an additional fee. (Note:
additional fee not reflected in final price listed below).
3. Replace all oxidized metal flashing, cornice, and all other required spots in various sizes.
4. Completely sweep and clean around roof projections and other installations
APPLICATION:
Install 2” x 2” cant strip all around parapet walls.
2. Install 1-layer of 28lb. fiberglass base felt.
3. Install APP NB 80 base via torch down.
4. Install 1-layer of modified bitumen polyester roofing materials with a torch, following the
procedures for heat-welded systems.
5. Replace sheet pipe collar and base flashing for all vents.
6. Replace all sheet metal work (noising, flashing, etc.)
7. Replace main drain outlet, downspout, and conduct head.
8. Replace chimney (x2).
9. Apply silicone coating to or replace light well area with modified bitumen.
10. Reseal all around the roof projection and completion areas with roof flashing compound.
11. Examine and clean exterior entrance roof and apply sealant if needed.
12. Clean debris and garbage generated by our work.
WARRANTY:
– A Tech Roofing provides a 10-year warranty on the work included in the above
proposal.
What are your thoughts about this roofing material, color, estimate, etc.?
Also, I am seriously thinking of insulating the roof at the same time as replacing my old roof. (My home has no “attic.”). The roofer I referenced usually doesn’t install roof insulation due to the city’s mild climate. He recommended the 0.5 in fiberboard, but your article is strongly against this choice, correct? What would be your insulation recommendation?
Of course, please provide any, other suggestions or information about what you believe may be the best approach for my San Francisco home.
Thank you.
Julie
Flat roof in South Florida… iso board on top w roll roofing over…. 2×8 “crawl space” with fiberglass batts installed…
-Problem… inside the units get cold like 70 degrees… condensation appearing on the “crawl space” side of the drywall…mold growing like crazy…batts are trapping moisture I believe….
-Fix… demo ceiling,remove batts, attach xps 250 foamular to fir strips, make air tight,then attach drywall…
Question: how to determine the thickness of xps to eliminate condensation. I understand dewpoint, but not sure how to account for proper R-value to cause right temp difference from inside room(70 degrees approx) to outside temp/relative humidity(approx 86/62%.
Is there a formula you know of good sirs?
Forrest – I’m not a big expert on condensation, especially that I’m in north east, and don’t have much experience with Florida-specific issues.
That said, from much research, a closed cell spray foam would probably make a great vapor barrier together with 6R / inch insulation value, which is higher than XPS, easier to install between rafters, and much CHEAPER than XPS. You should probably consider it.
Keep in mind, that OPEN CELL is not a vapor barrier, and will be soaked, based on what I read in some research paper on moisture/vapor in the southern states, and spray foam.
XPS will not create a “seal” so the moisture will still move through the roof structure. So I think XPS is a waste of money.
Hi
I’ve got a 2500sf small commercial building in Lombard, Illinois. All flat roof. 2×12,s at 12” c/c w/ 3/4” wood decking. Can I insulate under the decking in the building in the cell spaces and not insulate the roof?
Or, do I insulate the roof deck and leave the inside without batts? Where would the vapor barrier go?
Thank You.
John
I think I made a huge mistake in repeating the insulation method of a previous contractor. The layers from inside out- drywall, krft faced, batt insulation 6″ in between 2X12 joists, Roof sheathing, poly iso then epdm ballasted.
My first flat roof…lucky homeowner
the previous joists and plywood rood deck in this room –which is a 140 sf bathroom
I assumed that it was leaking in from above and rotted it out. It was rotted when I bought the property.
Hired an experienced commerical flat roofer and they admitted not knowing but suggested it was from above the deck leaking in. But after studying this a bit, I am starting to think it was condensation that rotted out the roof deck and joists
There was never a wet spot in the ceiling of the bathroom even after it rotted through. The builder had insulated same as I described above except instead of kraft faced he covered it in heavy plastic vapor barrier before drywall was installed
No one investigated too much since it was a reroof.
The last roof above the bathroom was definitely rotted out by the 15th year after initial install. The house is old but the bathroom was an addition that involved a new roof
I am not certain if the new roof I had installed had vapor or air barriers above the roof deck in addition to the layers I described.
Any one see instances where insulation from below the roof deck and poly above leads to condensation rotting out the wood deck and joists? House is in a very cold climate-Minnesota
Hi, I’ve got a TPO roof in Albuquerque (1600 sq ft) that needs repair. My roofer says 1/2 inch APS insulation is sufficient. I’m thinking more insulation would be better but I can’t find good guidance on this. Thoughts? Thank you!
N. Shaw,
I think there is almost no situation when more insulation would not be better. The more, the merrier. I would say 3-6″ of PolyISO is bare minimum for a roof. That would be 18-36R … Most building codes suggest 48R or more.
The issue is – you already have your roof installed, so either you somehow can get spray foam insulation under the roof, or need to remove the roof and install insulation, and then new roof.
Good luck.
Hi Leo,
I have a 30′ 1953 mobile home with a curved roof that looks like a classic spartanette camper. The roof is rolled steel that has multiple layers of various brushed on coatings that are dried and cracked. On top of that is a rubber roof which was added at some point, that was glued and poorly fastened at the roof edges. I am carefully peeling back the rubber to scrape off the cracking coatings and trying to decide how to best protect the roof. The steel roof has areas of rust and at least one place is rusted through. Since the rubber is still in good shape I am considering fastening a single layer of polyiso panels to the steel roof, then gluing the rubber roof to the polyiso. Does this sound OK? Other options?
Hi Leo – I just saw this thread and am hoping it’s still active. I have a 14 year old 2000 sq. ft. house in the Albuquerque area and am told that I need a new roof. What I have is a BUR (one layer); it has been periodically been checked out and repaired in the past, and it was determined to be OK recently as last year – but I have to say this opinion was not given by a licensed roof professional. I realize nothing lasts forever though and am ready to bite the bullet and get a new one. The one estimate I’ve gotten so far however has given me sticker shock: $26,000. This is at least twice what I expected and significantly above what any of the sources I’ve found on-line say, which is that reroofing my BUR roof over a single previous one ought to cost no more than $7.00 per square foot. Are all of those sources equally wrong and by the same amount? I’m flabbergasted. . .
Hi Steven,
So first, a technical correction – BUR which stand s for Built-Up Roof, by its nature cannot be 1 layer. Its multiple layers built one on top of another (usually 3-4 layers). BUR can be Modified Bitumen over a cap sheet and/or base sheet (2-3 layers) or hot-mopped tar (with or without gravel) – again, multiple layers of fiberglass mat, mopped with tar/asphalt.
Reason I’m explaining this, is to show that BUR roof can pose an issue with extra roof weight, if it is not removed during new roof install.
Being in New Mexico, and roof being only 14 years old, I doubt it is a BUR roof. BUR is not a common roofing material in your neck of the woods (or should I say desert) 🙂 …
My guess, it is some sort of membrane (EPDM, PVC, TPO, etc) or Spray Foam insulation Roof. But of course i could be wrong. Also, EPDM is unlikely in NM, since most of it is black.
Another guess is that your “roofers” really did 1 layer of some sort of Modified Bitumen, perhaps over a felt paper, and that could be referred to as BUR…
Anyway, to answer your question on costs.
#1 – in 2021, roofing MATERIALS costs went up somewhere in the range of 30-50%!
#2 – thanks to Covid unemployment checks (which just recently stopped), roofers and many other contractors were really short on labor, as workers chose to just stay home and collect Covid pay. Literally, 100s of thousands if not millions of construction workers refused to go to work, even when offered cash under the table, so they would not lose their Covid payments, or just because it’s more fun to drink beer all day and not have to work.
#3 – This left a significant backlog of jobs that could not be completed on schedule, due to workers shortage. As a result, contractors started picking easier and higher paying jobs. Now customers have to compete over contractors, resulting in overall increase in installed costs of roughly 25-30%.
One example is Zillow, which paused its iBuyer program, primarily because of labor & materials shortage.
This brings us to about $9-10 per square foot of simple flat roof, done with something like a 50-60 mil TPO/PVC, and before accounting for any extra work (such as skylights, tear-off, wall flashings, etc).
I don’t know the specifics of your roof, and whether you have any of those extra work items. But now in the end of 2021, I would say that $10/ft is not out of the question, and given that your roof is 2000 sq.ft. (or more, if you have overhangs, etc), $20,000 price seems within the reality.
Now $26K is a bit too much I think … but if your 2000 sq. ft. home has a 2′ overhang all around (say it is 50×40′) … the 24″ overhang will add almost 400 sq.ft. to the mix…
If you want, provide some basic description of your roof, and perhaps a few pictures uploaded to Imgur.com, and I will let you know what I think.
Good luck.
I live in northern utah and have a flat roof with a membrane. I am replacing the ceiling drywall and wondering if I should be replacing/ adding new insulation. There is only an 8 inch gap in the rafters from drywall to the roof. I have found conflicting advise on weather i should be putting bat insulation in this space due to condensation issues. Do you have guidance?
Did you get a response to your concerns? I’m also in northern utah and having to face the same ceiling insulation matter.
Is it common for flat roofs with a 2″ insulation on top of the deck be covered with modified bitumen without adding plywood on top of the insulation boards? That’s what I’m seeing on my friend’s roof and now that it needs to be re-roofed with TPO, the tearing off of the old mod bit material is stuck to the insulation boards therfore the foam boards have to be replaced as well. Shouldn’t the insulation boards be covered by plywood before applying the mod bit material?
I have a home that has an original flat roof that a metal roof has been permanently installed over it with 2×4 pitch and supports. The home get extremely hot and the a/c cannot combat it. What is the best method to add insulation?
Linda,
I think the simplest and cheapest option is to use a white urethane coating, that will reflect most of the sun heat.
Another option is to install PolyISO insulation (about 3″ thick) on top of metal and do a PVC roof on top. This will be a lot more expensive, but will give you insulation value of about 18R and white PVC will reflect upto 95% of solar heat.
Third option is to upgrade your AC to to a multi-zone ductless mini-split system, which is a lot more efficient that old central AC systems. When I say efficient consider this. Your old AC probably is at most 13 SEER. If it is over 10 years old, it’s likely 8-9 SEER.
Also you lose 30% of cold air in the ducts, so effectively you are left with 6-7 SEER.
Ductless 4-6 zone systems (from Mitsubishi / Daikin / Fujitsu) will have about 20-22 SEER, which is measured in the room (not in the basement, so no losses in ducts) and is 3 times more efficient. Therefore you will use 3 times less electricity.
Here is the math (BTUs / SEER = WATTS):
If you have a 3 TON or 36000 btus/h system (good for about 1500-1700 sq. ft. home), at 13 SEER the system will draw 2.77 kW.
Same size older AC at 9 SEER, your power draw will be 4 kW.
A 20 SEER ductless system of same 3 TON size will draw 1.8 kW.
So if you run your AC 10 hours a day, and your electric cost is $0.12/ kWh (US average), your usage will be the following:
13 SEER AC = 10 hrs x 2.77 kW x $0.12 = $3.324 / day or $99.72 / mo.
9 SEER AC = 10 hrs x 4 kW x $0.12 = $4.80 / day or $144 / mo.
20 SEER Ductless = 10 hrs x 1.8 kW x $0.12 = $2.16 / day or $64.8 / mo.
So going from old AC to 20 SEER ductless will save you $79.20 per month in electricity. Depending on where you live, you may run the AC 100-200 days (3.5-7 months) a year or more. So yearly saving can be around as much as $1000/yr. If your electric cost is similar to what we have in Massachusetts ($0.24) your savings would double.
And this assumes that you run all your zones at the same time for 10 hrs a day, which most people will not do. So you will likely save even more than that.
Bottom line – I think the most effective way, without knowing much about your roof, would be to do white Urethane coating (cheap and effective) and consider upgrading to a ductless system, or possibly a Central Heat Pump. Central Heat Pump is not as efficient as ductless, but will be cheaper to install, and still a lot more efficient than old central AC systems.
Good luck, Leo
I live in South Florida approximately two miles inland from the Atlantic ocean. My house needs a new flat and (low slope) shed roof to replace the current tar & gravel one. The ceiling in the living room, carport and all of the 3′ overhang around the perimeter is exposed 1″x8″ T&G.
The first issue is that any roofers that have taken a look say they would use 3/4″ nails to attach the anchor sheet because apparently that’s shortest nails available for roofing nail guns. When I suggest hand nailing with 5/8″ they look at me like I’m crazy. I understand that the nail is going through the 75 lbs. felt and a tin tag first. However, even if the nail doesn’t come through it could most likely dimple the underside of the varnished ceiling.
The second is a question is about the proper way to hot mop the remaining layers over Poly ISO? Is GAF perforated stratavent a good option or is using a 1/2″ cover board better? Using the Startavent seems like it would save with time and materials. However, the quotes I have received do not reflect this.
Any suggestions would be greatly appreciated.
Kurt,
I understand that aesthetics or visuals of the 3′ overhang are very important to you, BUT, here is very important technical aspect that trumps your aesthetic desires:
Nails MUST penetrate wood by 3/4″ … Not be 3/4″ or 5/8″ long …. they have to come out of the wood by 3/4″. That is extremely important if you don’t want your roof to fly off in the next storm.
The way to deal with it, is to add a suspended overhang soffit … attach 2×2 battens, and runs a course of 1×8 tongue & grove boards. This will give you the visuals that you desire, and allow roofers to properly install the roof.
Also, living if Florida, why would you want to install a new hot-mop roof???
There are excellent single ply membrane options (I recommend PVC roof form IB or Sarnafil (SIKA) or Cooley. These are great product that will last for decades, and reflect 95% of solar heat, keeping your house much cooler. Cost wise, there isn’t much of a difference.
Since you live within 2 miles from ocean, I would recommend stainless steel edge metal (over galvanized). IB has the stainless options, while others do not. However, it is not necessary, as in many cases, membrane is folded over the roof edge and a decorative aluminum trim is installed.
Now about your 2nd (Stratavent) question – that only applies to modified bitumen from GAF, and since I suggest going with a completely different product/system, Stratavent does not apply. But to answer your question – according to GAF, Stratavent sheet should be installed directly over POLY ISO … I did not see mention for “fiber board” … if “1/2″ cover board” that you refer to is fiber board, you probably should not use it.
Also … the savings that you want to see are “visible” in large commercial projects, where total cost is $500,000 and up … I don’t really know how math on that would work for a small residential job, but probably you would not see more than $200-300 in savings.
Bottom line – I recommend you abandon the idea of going with modified bitumen roof, and go with quality single ply PVC roof. GAF would not be one of those “quality PVCs” … GAF is primarily an asphalt/epdm manufacturer, and while they do sell PVC, I would still use the 3 products I recommended above.
Good luck
Exposed ceilings are very common in older Florida homes. I contacted my local building department and they told me that exposed ceilings require an enhanced tin cap nailing pattern per Code. The rafters are tin-capped with 1 ¼” roofing nails every 9” and the remaining field is then capped every six inches with ¾” nails.
I will also use a GAF #80 Ultima Base Sheet that I believe is slightly thicker than the typical #75 to avoid any dimpling on the underside of the ceiling. The hot mop system is used to adhere the poly ISO + multiple layers offer more redundancy if something where to hit the roof during a hurricane.
Thank you for your suggestions and advise.
I am buying a home where a pitched roof was installed over a flat roof, kind of like the lid of a cookie jar. What concerns should I have about the original flat roof that is still intact underneath? And there is no insulation in the pitched roof, should that be added?
Nicole,
Honestly there are so many things here to be concerned with – I don’t know where to begin.
1) Was the job done by code? Where building permits pulled? Is flat roof load bearing adequate for the added wight of sloped roof on top?
2) As far as insinuation – if your flat roof has it, you don’t really need it on the sloped part. What you do need is ventilation of the sloped part.
Honestly not seeing the roof in person, I would just recommend staying away from this house all together.
I also think it is a pretty stupid approach to build sloped frame on top of flat roof, just because a roofer was too dumb to make the flat roof not leak. It’s a great waste of money…
Good luck
Thank you for taking the time to read this.
im considering building a home with a flat roof or slope roof in new jersey. our temps change often from botttom to top of roof what materials should i use the roof size is going to be 26′ x44′
kindly,
Steve
so glad I found your site. we’ve had a new 60 mil gaf tpo roof system put on our house. the house has a 1/12 pitch roof. cathedral without any attic space. a 1.5 inch polyiso insulation was installed under the tpo with a 2×4 boarder as a nailer/support. as it sits i
I have an insulation factor of about 8-10 plus the reflectivity of the white tpo. is there any advantage to trying to get any insulation in between the 2×8 rafters. the old roof was tar and gravel so the switch to tpo should show significant change. also there is a soffit vent but none at roof peak. should I leave out the soffit vent.
Thanks for your time,
John Russell
Hi,
My roof has a ponding issue, my roofer wants to put 1” tapered insulation to correct this problem.
However another roofer advised me not to put tapered insulation.
What is the best way to go because our association cleans and repaints our tile roof 2 times within 6 years.
I’m afraid of the damage that would be caused with the insulation when walking on it ie; leaks, punctures, since it is styrofoam.
Also do you suggest having the roof sealed once it is replaced.
What are the advantages and disadvantages of the insulation for ponding issues.
Ft Lauderdale Florida
I have serious roof damage. You know the kind you can’t see and all of a sudden everything come apart.
On the roof can I put something down between the sheathing and the roof material as a thermal brake. To get ride of the condensation that occurs ( hot outside cool inside and in winter cold out hot inside)
Antonio,
There are NUMEROUS WAYS to approach this (insulating the roof/attic).
The most common is to put baffles (to allow ventilation) between rafters, and then put fiberglass insulation you should go with at least 30R insulation.
If you don’t have access to rafters, you can put blown in insulation of fiberglass or a number of board insulation types on the floor of the attic, between joists, an then the attic space itself will be “cold”.
If that’s not an option, you do several types of roof-top insulation. These can be done ONLY when you are replacing your roof, and require removing of old shingles!
1) Get insulated panels with OSB board attached to ISO insulation – you will then screw this over current roof deck.
2) Cold Roof: Run vertical 2×3 boards (battens) over roof sheething, ~ 16″ O.C. and then install 1/2″ (minimum recommended is 5/8″) or thicker plywood on top of battens). This will create ventilation and separation between attic/roof substate, and the roof itself.
3) Screw in 1-3″ of ISO insulation over roof substate, and then install plywood over ISO boars… same as #1, but more work.
Then you should use GAF DeckArmor which is by far the best synthetic roof underlayment at reasonable price (about $0.22/sq.ft.). DeckArmor is not only great at preventing roof leaks (when installed correctly!!!), but is also breathable, and will let moisture from the attic to escape, where as 99% of all other synthetic underlayments are VAPOR BARRIERS – non breathable, and will trap moisture.
I hope this answers your question – Good luck!
Leo
I live in New Port Richey Fl in 55+ condo community built in 1974. It has a flat roof with mansards. Recently had a leak which showed up along the ceiling and wall on 2 edges of one of my bedrooms. The roof was repaired and they sprayed some kind of solution on the brown spots rather than replacing the wet drywall. The attic has batting and some blown in insulation in it. Sine I purchased this house in 2016 there has been a very musty smell. I’ve ran a humidifier continuously but the smell remains. Need advice on if the insulation should be removed and the proper repair of the drywall Thank you!
Carolyn,
You are likely having a problem with poor attic ventilation. Do you have attic access?
It is a good idea to add Soffit/Ridge vents if possible, or perhaps even a power vent (solar powered, so you do not need to run electric wires to it).
After you fix ventilation, see if your smell and ceiling situation improves. If you have further questions, feel free to reach out.
Good luck.
In August of 2016, I had a relatively flat roof (1.5 in slope per foot) built for our 1500 sq ft addition. It has spray foam insulation entirely with 8″ joists. There are soffit vents and a ridge vent but then the foam occupies the entire cavity anyhow. Now in the intense 100 degree heat of this summer of 2019, the roof is melting. The underlying adhesive is running down and dripping off the edges onto the patio. It is a mess. Everyone is pointing fingers at everyone else. Any information or advice would be greatly appreciated. Thank you.
I live in a 55+ condo self-managed. It has 120 units and 5 floors. I have been told once the building needs a new flat roof that we must add 5″ of insulation now. Can half a roof replacement be done and the other half in a few years or must the entire roof be done at one time due to new insulation mandated by the code? There are 120 AC units on the roof and 2 elevator ‘penthouses’.
Any idea cost of flat roof replacement in IL?
Hi Gail
1) You can do half a roof at once, and then complete second half later.
First of all, it is crucial to select proper material fo the job, especially give that it will be several years until you do second half of the roof. Critical part here is – will you be able to create a watertight joint in 3-5 years.
For this I recommend that your condo goes with quality PVC roofing. This will allow you to easily create a watertight joint later on, and not worry about product compatibility. Virtually all PVC can be fused together even after 10 – 15+ years. I cannot say the same about TPO, because no one knows what will be the formulation of new TPOs in 5 years (even the manufacturers), and compatibility may be an issue.
EPDM rubber I outright DO NOT recommend for many reasons.
Check out this flat roof guide to get more information on different materials, and why I recommend PVC.
The important part here is to make sure that seam between old and new roofs is water tight.
For that, your roofer should build a small “wall” at the edge of 5″ insulation … pressure treated 2x4s will suffice. Then, run the old roofing material all the way up and a little bit over this “wall”, and overlap it with new roofing material. Terminate old roofing into the vertical part of this wall. It’s ideal not to make any penetrations on the horizontal plane.
Later, when you do second part of the roof, I recommend adding another layer of 2x4s to the wall, to create a proper future joint. However, this may be an issue if the water should flow between the two roofs – then you do a flat joint, and just weld the seams of old and new material.
What type of AC units do you have? A free-standing condenser coil OR a large curb-mounted AC? I presume free-standing ones, as it’s pretty insane to have 120 curb-mounted ACs 🙂 In such case, there really isn’t any flashing required – just put a piece of matching roofing material under each pedestal.
As far as costs, you need to provide square footage of the roof. However, if we do not include removal of old roofing, you are looking at about $7.50 to $9.00 per foot of Roofing, plus about $2.50 to $3.00 per foot of 5″ thick Insulation … say about $10-$12 per square foot.
Each elevator shaft should not cost more than $500-700 to flash.
Ideally you should estimate more accurate cost with our flat roof cost estimator.
PS, I am not sure that you are in fact required to go with 5″ insulation on a retrofit job (usually these requirements apply only to New Construction), but each state / city have their own requirements. Regardless, it is a good idea to have as much insulation as possible, until you get to a point of diminishing return (above 50-R or 8.3″ of ISO insulation).
Good luck!
Leo,
Thank you for taking the time to give us your professional advice. We have an email out to the contractor asking why he took it upon himself to change the materials without informing us and he has not yet responded. Your response confirms my husband and my research on the materials. It really disappoints us that we had faith in this contractor and now have to confront him on such a matter. Fortunately we did not pay in full. We intend to negotiate.
Thanks again,
Karen
After requesting a new flat roof system to be installed with new decking where needed plus 1″ polyisocyanurate insulation and .060 EPDM we received a Quote from a contractor that was within our budget. We asked for these products due to the insulation value and quality. One half of our roof had been done using these products in the past and we wanted it to match. Instead of using the polyiso boards they installed two 1/2″ layers of fiberboard staggering the seams. When we questioned him about this type of cover boards he informed us that this would be a better system then using polyiso boards. He mentioned several times that by staggering the seams that this method would be better. We are having our doubts as to this being true. Our research tells us that this will be less then half the insulation value. Now we are questioning the rubber that was used?
Our question is , will this installed roof be less in value (in more ways than one) then the roof we thought we were paying for?
Karen,
If your contract says 1″ Poly ISO, that it’s an outright scam, and I recommend you don’t pay the full amount owed. And not even the difference in cost between 1″ ISO and 1″ fiber board. Because in reality, you wanted to get ISO for insulating value, and fiber board has about 1-R per inch, while ISO has 6-R per inch. So even if you pay less in the amount of price difference between fiberboard and ISO, it will cost you much more to add that missing 5-R to your roof.
Bottom line, contractor is an idiot and a lier. Fiber board is not better than Poly ISO in any way, and staggering sheets does very little to increase R-value.
This situation seem quiet ridiculous because the “savings” for the contractor would be $0.15-$0.20 per square foot. Even if the job is 2000 sq.ft. (which I doubt), total saving of $300-400 is not worth issues with the client.
I’d suggest you make them remove the rubber, replace fiberboard with ISO, and use NEW rubber (not reuse the material which they would remove). They will most likely refuse to do so. They you should refuse to pay the final invoice.
If it comes to that, they will likely attempt to put a mechanic’s lien on your home, which you should fight, stating that contractor did not install product according to contracts.
Best of luck. Leo
I am interested in your option . I have a flat roof I need to get to r 49
Mark,
8″ of POLY ISO will give you 48-R 🙂
If you have parapet walls, you are in good shape. Otherwise you will need to build up a wood nailer around perimeter. Insulation can be attached with special order 9-10″ screws. Membrane can be glued over.
There may be a slightly more dense insulation, but the most you can get is 6.5-7 R per inch, so still ate least 7″ thick.
Good luck – that’s gonna be pretty expensive.
I live in southern Ontario Canada, where there are significant differentials of temperatures from summer to winter. We are insulating a flat roof with tapered rigid insulation over a moisture barrier, and then capped with modified bitumen. However, we lose R value where the taper is thinnest, and need to insulate under the sheeting. We toyed with spray foam, but this may be overkill as we would have to insulate areas that don’t require it. So, we are considering packing the rafters, which are only 12 inches, with 12” fiberglass insulation to remove any airspace. A gentleman from IKO suggested that this would be fine provided that we don’t add another moisture barrier, but I would like another opinion.
Cheers,
Mark de Wolde
Mark, why not add another 2-3 inches of non-tapered ISO below tapered? The way I look at it – tapered is for roof slope/drainage, and while it’s expensive, it’s cheaper that building a sloped frame. Insulation is an added benefit but not main purpose of tapered insulation 🙂
Adding 3 inches of ISO, will give you 18-R throughout the roof. And where tapered ISO is the thickest, you will have more. Cost per foot of 3″ ISO is about $0.9-1.00 for materials. I don’ts see this increasing labor cost too much as your roofer is already doing insulation. I think this will be more or less comparable with fiberglass, when all is set and done … unless you have easy access you the 12″ rafters … then fiberglass would probably be cheaper.
Finally, I do not think that fiberglass will affect moisture properties much, as it’s not a moisture barrier…
Bottom line – see what is most cost efficient for you.
Good luck
My fiance and I moved into a new home recently and we want to get better roof insulation. We are interested in the different types including flat roof insulation. It is nice to know that we can prevent rotting by making sure we have ventilation.
My mom lives in Northern WI with a flat roof. We don’t think it has insulation!! Because 4″ of ice builds up during winter. It’s covered with that black rubber liquid.
Can insulation be blown in from the sides without taking off the rubber top layers?
It’s a 1200 sq ft house.
Thank you
Happy winter
Amber,
Flat roof rafters usually run from high point to low point. So any blown-in insulation needs to be installed from top or bottom (whichever has better access). You cannot add insulation from the sides.
That said – if there is space between rafters, where you can “snake” a 3 inch hose in, all the way to the other side, then sure – you should be able to do it.
You will need to locate all rafters and drill approximately 3″ wide holes between every rafter. Then just push the hose as far as you can. I would measure roof run and measure the same distance on the hose. Add a couple of feet, and put a tape around it. That way you will know how far your hose went in.
It should work, and is definitely a good measure. At the end, I would just replace the fascia board (the one with 3″ holes, or at least fill in the holes, and install flat stock aluminum over it, to cover the holes.
Potential issues:
If your roof is leaking – you will just waste time and money. Also this MAY create ventilation issues.
Good luck
It sounds like remembering these four myths will get you better quality and save money when installing insulation for your roof. I’d imagine it would also keep you from investing into a scam.