EPDM rubber roofing may be very cheap, but there are a number of disadvantages to EPDM roofing a homeowner should be aware of, before choosing it as membrane cover for their flat roof.
From the perspective of quality and longevity, EPDM rubber roofing is one of the least reliable flat roofs.
To get started on installing a quality flat roof, contact your local roofing pros for FREE ESTIMATES!
Top Disadvantages Of EPDM Roofing
It may come as a surprise to you, but the roofing industry often misleads and misinforms consumers into buying products designed to FAIL within 15 years or less.
This is happening in an effort to keep up the demand for production of new materials, as well as the demand for roof replacement (just like old-time furniture makers would put bedbugs in new mattresses).
This mass deception based on the promises of long warranties and low prices, is called “effective marketing”.
We are not the ones to judge, but we would like to shed light on what is really going on in the residential rubber roofing materials market.
Average Flat Roof Cost:
Low End
$6815
|
Mid Range
$8769
|
High End
$11211
|
|
1. Unprofessional Contractors = Poor Residential Rubber Roof Installation
Many contractors praise and install the EPDM roofing system, because manufacturers that make this material do not require roofers to be certified or trained in order to purchase and install it.
Furthermore, rubber roofs are CHEAP. There are no special tools, or equipment required for installation. Some $1 paint brushes and a $15 hand-roller is all that you or a roofer would really need to get going.
EPDM is also easily accessible. Anybody can get all materials and accessories at a local home improvement store. You also don’t need to purchase very large quantities, (as you would for most other materials).
All of the above factors combined with eager cooperation on the part of distributors, promoting this roof at “special seminars”, creates a situation where poorly trained contractors put up a “rubber roofing” sticker on their trucks, and set out to get some business.
Homeowners, who are unaware of this situation, usually believe that they are dealing with qualified professional contractors. Although, these roofers may know how to shingle a roof and may even have good references, chances are that their expertise with a single ply membrane is limited, or non existent.
It is important to realize that a flat roof is a completely different “animal” and not every contractor can properly install, or repair a single ply membrane. Furthermore, there are many fly-by-night roofers who will do the install dirt cheap, and when the roof leaks you will never find them.
Here is a great example of a “Professional” flat roof installation – the membrane glued directly to asphalt shingles: EPDM material should never come in contact with asphalt-based products, and it should be installed over insulation, or fiber recovery board. This roof is leaking in 7 different places.
2. Seams Failure = Leaks
Here is an industry fact that most homeowners don’t know – even when a rubber roof is installed correctly, it will most likely still leak. This is because it is designed to have seams that are glued together, effectively keeping it watertight.
Over time, even the best glue dries up and fails in 7-10 years or sooner, allowing the seams to come apart. At that point, the roof is left completely vulnerable to water infiltration.
The worst part – this is an unavoidable systemic problem with the design of this roof. The best you can do is prolong the period before the seams fail. But, they will eventually fail, nonetheless.
This is why if you want to avoid recurring leaks, it is best to install a seamless single-ply membrane, such as PVC or TPO roofing.
3. A Rubber Roof Membrane Will Inevitably Shrink = Leaks
Another inherent design problem is that after a few years, this roof membrane simply begins to shrink, slowly pulling away from parapet walls, flashings, corners, drains and other areas. At that point, leaks start penetrating these weak points. Shrinkage is a particularly serious problem on a larger size roof.
4. EPDM Rubber Roofing Requires Regular Maintenance
If your flat roofing membrane was installed correctly, you will still need to perform regular maintenance to avoid leaks and get the maximum service life.
Because the seams can start to come apart, they need to be inspected at least once a year to ensure they are in tact, and speedily repaired, if any problems are detected.
Such an inspection can cost around $300-550, depending on where you live.
After about 5-7 years, you will have to reseam your roof by installing a 6-12 inch wide EPDM cover tape over the old seams to make sure they don’t leak for the next few years.
This update will cost you about $10-15/linear foot, so if you have a few hundred feet of seams, the total cost will be several thousand dollars, making it a very expensive maintenance program.
If your rubber roof develops small leaks, hiring a contractor will cost you $400 or more. Alternatively, you can do the repair yourself using a DIY Repair Kit, like this.
Average Flat Roof Cost:
Low End
$6815
|
Mid Range
$8769
|
High End
$11211
|
|
5. EPDM Rubber Is NOT An Environmentally-Friendly Material
If you care about the environmental footprint left by the materials you use in your home improvement endeavors, you would want to stay away from EPDM roofs.
Rubber is considered one of the least eco-friendly materials in the industry. It is manufactured primarily from oil-based byproducts, such as ethylene, propylene and others.
Thus, it requires heavy energy consumption during the production phase, supports our country’s dependence on oil and increases green house gas emissions.
Black color membranes (most common and cheapest) are not energy-efficient, because they attract UV radiation from the sun and raise the ambient temperature inside the house.
This means that you will spend more on your cooling costs during the summer months. Poor energy efficiency will be most pronounced in regions with hot, sunny weather, year round.
Average Flat Roof Cost:
Low End
$6815
|
Mid Range
$8769
|
High End
$11211
|
|
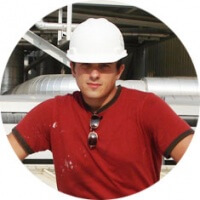
For over 20 years Leo has run a successful roofing business in New England, specializing in metal roofing, as well as cool flat roofing technologies. Having replaced and installed hundreds of roofs in New England, Leo has first hand experience with pretty much every residential roofing material and roofing manufacturer available in the US.
Thanks for your post. It is interesting reading this and the comments that follow.
I have a very small flat roof on the back of my home (20′ x 9′ approximately). I am in the process of getting quotes to replace. The first company does EPDM.
Another company that I haven’t met with advertises that they use CertainTeed’s Flintlastic SA products. What are your thoughts on this? This is a self adhering modified bitumen product? I currently have a torch down modified bitumen. I prefer the look of modified bitumen over EPDM. The other materials you mentioned don’t seem to be very common in my area for this type of room (I am in the midwest).
Thanks!
David,
I am very familiar with Flintlastic, and similar products from other manufacturers, as well as modified bitumen in general.
Flintlastic is a cold-applied mod-bit (no torching). This is good and not so good at the same time, but is more of a theoretical thing.
As far as your roof – does it have any slope? Are there any protrusions? Any skylights?
If it is a completely flat (no penetrations) roof, and has at least 1/12″ slope, you can do either EPDM or Mod-Bit (Flintlastic), or PVC or TPO …
If you have falling tree branches, Flintlastic is better, as it is much more durable.
If not, and you chose EPDM, make sure it a single sheet (10×20′) and there are no seams.
If you have penetrations, or no slope is – definitely not Flintlastic. You can do PVC or TPO, or maybe EPDM.
I hope all this makes sense. Let me know if you have further questions.
Good luck.
Thank you for your reply!
My flat roof has no slope and no skylights or anything else.
Since there is no slope, Flintlastic is out? I currently have a torch down modified bitumen.
Seems EPDM is popular in my neighborhood, where most houses have these flat roofs.
Thanks!
I professionally installed EP DM, TPO, and PVC roofing along with built up roofing for 24 years. If you have a professional ““ do it, you should have a very good system that can last a very long time when the right products are used. Lots of factors need to be taken in as far as what is going to be affecting the material on the roof such as grease if there are in a restaurant setting or other environmental factors. Determining whether PVC or TPO can be used en lieu of rubber as an option.. The problem is not the materials in most cases, it is the installation process and the contractor. In any setting when these two things are not competent, they will fail. If you’re the type of person that likes to do things yourself around the house and think that putting on a rubber roof correctly is an easy task, you need to think again.
Hi, I wonder if anyone could advise me regarding EPDM roofing. I was considering having a flat dormer roof recovered with EPDM and asked the company supplying me with a quote if it was susceptible to damage by embers from the log burning stove I have installed. I was not convinced with the answer I received, stating it would be perfectly fine and not be harmed. After reading the information given on this site I am now certain EPDM is not for me but I would like to confirm that the answer I was given was incorrect. If they can’t be honest I can’t trust them to carry out other work I had planned for them to do. Thank you.
Brian,
To start, I am biased when it comes to flat roofing materials, and my opinion is that EPDM is junk, any way you look at it.
PVC roofing will not burn on its own (if there is no source of flame). TPO will burn, and so will EPDM.
However, if you have burning ash flying out of your smoke stack, it is a problem and a fire hazard, regardless of the roof type. Maybe, fix that one first.
I hope this helps. Good Luck
I had a 60 mil epdm roof installed on a 3500 sq ft building 30 years ago, it is still ok. I did tape the seams 20 years ago myself, easy to do. I have a wood stove with a chimney 8 feet taller than the roof with a spark arrestor on it and have never gotten a burn from a cinder. Forth of July and the kids next door with their cheap Chinese fireworks however have landed a few that did leave a hole which needed patching. I am thinking of rolling a white silicone rubber on to extend it’s life a few more years and make it cooler. The only leaks were from a poorly designed rain gutter that I got rid of this year.
Leo-
Thank you for your excellent article. I particularly appreciate you allowing unedited replies to your articles, some of which may not agree with you. You’ve unintentionally created a forum which has attracted professionals as well as homeowners and provides a valuable exchange of information and opinions.
If you have a pitch to your roof why can’t the rubber be overlapped like shingles and enough to compensate for shrinkage over the lifetime? I just put on a 25 year architectural shingle with a peel and stick underlayment so that if I lose a shingle or two during a hurricane, the roof won’t leak before having a chance to replace shingles that come off.
Mike,
Rubber can be overlapped, but not with peel & stick underlayment, which is asphalt based and damages rubber over time. I mean it won’t destroy rubber right away, but it is not a good way to do it. I would use a synthetic underlayment just for overlap, and seal it to rubber with couple of courses of Solar Seal 900, and the you can put your peel & stick on top of synthetic, and install shingles.
Is it overkill? Yes.
Is it the right way to do it? Also yes.
Good luck
We have a combination pitch and flat roof so it feels confusing about which materials are best to use?
Hi Glenda
For flat roof, the best material is PVC membrane. And for steep slope most people use asphalt shingles. My opinion that metal roof is much better for steep slope, but it is expensive. So I would be an okay option
Hello, I was just curious to research for water tight surfaces;
I might add though –
if you are going to put “effective marketing” in quotes…
you should probably include the technical term >
“planned obsolesce”…
and yes it’s a drag on societies progress:/
+_yet_ until we can find a fix,
it’s also an ingrained part of Capitalism
and many markets-_-…
That said, it seems like this material
does better in some areas than others/
thanks all for your observations.
__
Farewell folks<3,
Dk
Or as a more permanent solution, you can go with a hot mopped or cold applied built up roof. If you want true longevity, that is by far and wide the way to go. I just made the first repair on a 4 ply hot mopped built up roof that was installed 42 years ago. Good luck getting any single ply product to do that. I believe a 2 ply modified bitumen roof with give better service than a single ply roof. When all of this single ply roofing became the rage, I asked an older roofer what he thought about it. He simply explained “Why would you put a 50 year roof on a building if you don’t know that you will be in the building 50 years.” I am a member of the National Guard and The United States Army Corps of Engineers, and guess what we put on our buildings-a 3 ply hot moped built up roof with a white granulated top ply. There is talk about moving to a Tremco cold applied built up roof to keep the fumes down. I have installed a few of these and they are a very tough roof.
The oldest roof I have ever had to repair was a coal tar built up roof that was over fifty years old. Coal tar is very rough product to work with, but I’m sure it’s the longest lasting “flat” roof out there. I have to fix them all, Ballasted EPDM, Fully Adhered EPDM, PVC, TPO, Built Up. There are advantages and disadvantages to al of the materials. But I know when its raining and I get the call to that 5 year old movie theater or 7 year old Home Depot with water running in the building, to grab the probe tool for that single ply roof leak.
Thank you so much for putting this information out there for us victims. You see I had my insurance agent out to check my 4 year young roof for damage from a mist recent hail storm but to my surprise hail is not the issue its the scumbag big wig roofing company that pulled the wool over my eyes to have me believe that my 2500 sq foot roof that cost over 15,000$ was shingles and lifetime warranty when in fact it’s rubber over shingles and leaking in numerous places on its 4th year…wtf…so of course when I call this scumbag co they can’t find my info and will look into it and call me back….that was 5 days ago…can you say scumbag meet my lawyer. Thanks again for this useful info
In most cases, you’ll need to let a professional handle installation to make sure that it’s done right. So, if you’re the DIY type, this is most likely a hands-off sort of project. This also goes for most large-scale repairs, although home and business owners can often handle small repairs on their own using EPDM Liquid Rubber. Roof protrusions and other potential problem areas need to be addressed before EPDM rubber roofing is installed to prevent punctures and other damage.
I have been doing rubber roofing for over 20yrs and I have roofs that I did that long ago still holding up to the extreme weather outside with out a problem. You see rubber and the supplies are not the problem it’s how they are installed period. You can get a 30yr warranty if u want n I’ve seen them last way longer than 30yrs.
I don’t agree with your thoughts. EPDM liquid rubber roofing is affordable, easy to install, durable, environmentally friendly and inherently waterproof, it is one of the best choices available for homes and businesses alike.
@ Victoria
I’m glad you are promoting you “product” on my website, and telling me how you “don’t agree” … not sure what it is that you don’t agree with – maybe you should tell us.
But right back at you – I honestly believe your “liquid rubber” is liquid rubbish! To me it is just like any other coating (it’s basically a thick paint), and if I was choosing to go with coating at all, I’d only use Urethane, and never on a flat roof membrane.
When (not if) your liquid coating dries up and starts peeling / chipping / cracking, like any other paint product, it will be impossible to remove it from the roof, and prevent any possibility of a repair, as patching material will not stick to the painted rubber.
Bottom line – you may push your “inherently waterproof” gimmick onto unsuspecting homeowners, but don’t come to a website ran by a professional roofer, and tell me that you have the “magic bullet”… especially passing off your self-promotion with “I don’t agree” line.
Good luck with your scams – i hope homeowners don’t fall for this.
Hey Leo! Hope you are having a wonderful day
Just a word to share with you that the liquid rubber is a BRAND.
The product is a two part system with the base being mixed with a highly volatile catalyst. Depending on application methods it can be put on and will cure without sagging to virtually any desired thickness.
So, I almost hate to get involved in this, but I can’t help myself. I fully agree with Tom and Joel. You are blaming the material for the work of amateurs and or crooks that don’t know the first thing about installing a rubber roof.
Let me get to the point about the seams first. No one glues laps anymore. We use in-seam tape. When you are talking about glueing/primering laps, you must of forgot to mention that when a lap is primed, a layer of 3” or 6” double sided tape is installed between the upper and lower parts of the lap. 3” tape is commonly used for fully adhered systems where as the 6” tape is made for loose laid roof systems where the rubber membrane is actually screwed to the roof through the laps with roof fasteners and 2” seam plates.
The 6” tape is made to provide total coverage of the 2” plate inside of the lap/seam, holding the rubber membrane to the roof.
Tape has been around since at least the 80’s and when properly installed, with low voc primer or prime-plus, those laps will not come apart. I will say however that I have been on plenty of roofs that were put together in the day when laps were glued with the actual flashing cement, and for the most part they held up pretty well considering the age and weather they had to deal with.
Most of the “glued laps” I have come across that failed, were put together with bonding adhesive, which any real roofer knows is not water-proof. I have been roofing for 20 years, 17 of them with a large scale commercial contractor who I was a foreman for 5 of, the rest running my own business, and have had the privilege of going back on jobs I worked on when I was 18 years old and still new to the roofing game, to fix holes that some HVAC guy carelessly put in the roof, and found the flashings of the curbs and the laps to still be holding up just fine. So the industry fact of how in 5-7 years the roof will leak is completely false. I’ve been on roofs that are older than the amount of time you’ve been roofing that still don’t leak.
As far as the shrinkage problem goes, once again you are blaming the material and not the installers. Yes the membrane absolutely will shrink. That’s why a real roofer uses perimeter fastening strip along walls and curb penetrations, or any place where there is an angle change in the roof. This holds the membrane in place and will not allow it to pull away from walls, curbs, etc. thus keeping the “shrinkage” that the roof will still experience, from becoming a problem.
The strip typically is fastened to the roof deck, over top of the insulation/backer board, and has a self-adhered tape strip on it. The membrane gets primed where it will stick to the tape, wall is rolled in, and then gone over with a hard rubber roller. As long as this process is done correctly,
I’m 99.99% sure you will not find it to stretch to the point where it rips the brick out of a wall. (They make perimeter fastening strip for tpo roofs as well for the same reason) While were on the brick wall topic, many roofs I have come across had been terminated here using termination bar. It failed. Know why? Because the installers did not put the necessary water block seal behind the membrane before installing the bar.
I have also been on plenty of roofs where this was installed correctly and have not found more than a handful of problems over all. Usually then it was because of careless hammer drilling and or installing lead anchors or screws that never held to begin with. These same things can occur on a TPO roof as well.
I have seen many roofers claim to know what their doing in all fields of roofing. From shingles to rubber, metal, tpo, slate, and so on. Very few have ever impressed me. Your comment on how buying a $2k welder and ten thousand dollar generator keeps the idiots out of that field is way off as well as I have seen plenty of idiots with welders in their hands that have no clue what their doing.
I have followed more than one “professional company” around that had these tools, probing their laps and flashings and ripping them right open. Why? Because when they weld these laps and so forth, they get them hot enough to stick for the initial probing but come back a day or two later and their already coming undone because the installers didn’t know how to weld. Typically this is called a “cold weld” as the inspectors around here refer to it.
I have even seen tpo roofs that had their flashings done with uncured elastoform and the laps put together with rubber in-seam tape. Funny thing is two of those roofs have not had a leak yet where as some other tpo roofs that were completely welded had many.
I have installed quite a few tpo roofs myself as well and never had more than a few problems, however I can say the same thing about EPDM. As far as fixing laps that are loose on a TPO roof, a lot of times the reason they are loose is they were either burned too hot during welding or not hot enough.
If they were done properly they should NEVER come apart. Hence the term “welding”. In a lot of cases re-welding these places is not going to work as the membrane was already over-heated. So then it needs patched anyway. Not a big deal if its just a spot here and there. But a lot of times its more than just that.
TPO repairs are not always just that simple either. The older the roof material is, the harder it is to get anything to weld to it. I know this from experience. We have had to do quite a few repairs on TPO roof over the years that were at the point that nothing would weld to it anymore and we ended up fixing it with rubber materials anyway. Some of these roofs were pretty old where as others weren’t any older than 5 years or so.
We have had to go back to jobs that were only a few years old as well to install new penetrations (hvac curbs, pipes) and couldn’t get the new membrane to weld to the old. And yes, it was completely cleaned with membrane cleaner. So we did the penetrations in rubber as well. Point is, every situation is different. Every roof system is different and if you choose the wrong product for the wrong location and hire the wrong people you will get crap that doesn’t work.
Honestly, I personally like TPO myself and enjoy installing these roofs. But there is other options out there. Try installing a TPO roof on a build-up roof tear off. There you have constant dust and dirt that gets on the membrane and affects the installation horribly, no matter how hard you try to keep a clean job site.
This whole post is like talking about how Ford is better than Chevy. Their all junk when their broke. If you want to educate people on roofing products than be fair about it. Don’t just feed people false information and try to make EPDM roof installers look like crooks for selling roofs that are according to you, junk.
Instead, make it known that EPDM is a fine product and the problem with all roofs is the fact that there are so so many bad installers out there that know most people don’t know what their looking at on their roofs. If its laying flat it looks good to them. And these bad installers exist everywhere from professional commercial companies, to small mom and pop companies. They sell every type of roof system from rubber and TPO, to shingles and metal. Opinions are one thing, facts are another. I am not usually the kind of person to get on a site like this and throw in my 2 pennies but I feel you probably are not that great of a roofer to begin with or you wouldn’t be trying to sell such a gimmicky roof by talking so bad about another that honestly has had a better run over all than you’re giving it credit for.
A truly great roofer will accommodate different roof systems effectively. 12 years ago Firestone told us that TPO was the way to go because in the next 5-10 years that’s all everyone’s going to be using. Well most commercial and residential work around here is still being done in EPDM for the most part. TPO is slowly making its way up the ladder so to speak.
TPO is not as great as you are trying to make it sound either, as a lot of manufacturers are still trying to figure out the best membrane formulation since many a TPO roof has had premature failures. There are reports on this. Failures due to everything from manufacturing defects to improper installation. 5 years ago TPO was very high on the single-ply membranes most problems list from the Roofing Contractor’s Institute. (Yes I just looked this up, though I didn’t have to since I have seen plenty of failed roofs myself.)
Finally, ALL flat roofs should have general maintenance as they are out in the weather. Things such as rain, sun, snow, ice, leaves, tree limbs, hail, and so on are always a problem for any roof at some point, and just like everything else, if you don’t maintain it, it will fail that much faster.
Roofer with a welder…burn all the laps on one job…move on to the next.
By the way, stow it with this “all you need is a paint brush and your a commercial roofer” crap too. The ONLY tools that separate the TPO roof from a rubber roof is in fact, the welders and generators. If you do a fully adhered TPO system your still using glue rollers and brushes just like on the EPDM. Still need screw guns for installing fasteners. Hammers to pound roof nails into edge metal. Still need knives and scissors for cutting.
Still use probes to check laps and rollers to roll seams and flashings. Tape measures, saws, hammer drills, tin snips for edge metal, etc. It’s literally the exact same process except all the details and laps are welded instead of flashed with uncured rubber and tape. A paint brush alone is not going to give you the necessary tools to install either roof and even the idiots have all these tools…..though most of them don’t know how to use them.
I encourage anyone who came to this post looking for information on EPDM to go investigate some ware else as this has not been good information. The TPO roof will cost you at least a third more, possibly more than that if someone tries to feed you crap about how much more technically involved this system is, and the only real benefit you will get from it is a roof that will more than likely be white instead of black which can actually help with heat reflection in the summer time.
Different roofing systems and specs also vary in different areas of the country as we obviously have different types of weather. Pick a roof that works for you, and do your homework on the roofer you hire to install it. It’s an investment.
@Ifioffendedyou ToBad – as promised, I’m replying in full to your excellent, and very long comment. Hope I don’t miss anything. I won’t answer all your points at once, but I will keep updating my reply, as I go through your comment.
1. (Mar. 12, 2019) Let’s begin with me “blaming material for the work of amateurs”. Here is how I see this issue:
a) It is impossible to consistently and reliably flash a 4×4″ railing post with EPDM uncured flashing. Even if you get the best 100 installers in the world, there will be failures, because the MATERIAL is just not made for this type of application. Any such flashing is what I call “stretch and hope” … stretch the uncured material to conform it to the penetration, and HOP, it sticks well, and doesn’t pull back. Most decent installers will have this fail at least in 1/10 instances… probably more.
Yet is is actively used and promoted for such use. This is just one of many examples, where rubber as MATERIAL fails in the flat roof applications. Also think of electrical wires coming out of the roof (pretty common) – the only way to flash this is with FLAT uncured flashing, wrapped around wires, and “LOTS of goo” (silicon, caulking, water-stop, etc) …
b) Both PVC and TPO have split flashings or square flashings designed for this specific application – no stretching and hoping.
Yes there are crooks and amateurs, but you also have them in any sub-trade of roofing, as well as in any construction trade. However, initial investment in Heat-Welding equipment, naturally keeps most of these clowns away from PVC / TPO, and they all resort to Rubber (since all you really need is a hand roller, and a brush).
At the same time, EPDM suppliers and manufacturers, create a situation where these clowns sell and install rubber roofs. They setup “training classes” for roofers, where one field tech shows how it’s done, while roofers sit around, sipping coffee, and after such 2-hour seminar, you are good to go, to buy and install EPDM … here is example of one such EPDM training.
2 – SEAMS It’s true that no one “glues” seams any more, and it is not even possible to easily buy EPDM glue. However – primer is in essence still GLUE. Sure the underside of Peel & Stick flashing has some sort of material that works together with primer, to create a better seal, but it is still glue, and those primed seams still come apart after a while.
3 – SHRINKAGE – Yes, manufacturers do recommend “base tie-in” method to prevent shrinkage, which to the best of my knowledge they “copied” from PVC / TPO. However, I personally haven’t seen this tie-in method used on Commercial roofs in Boston area more that once or twice. I honestly don’t even remember if I have ever seen it used in real life. And I too have seen many commercial roofs, that were installed by big and small, union and non-union Commercial Roofing Companies, These are not your run-off-the-mill shinglers. These are trained roof mechanics. In fact, I will go through my archive of commercial roofs, that I personally inspected, quoted and/or repaired, to find any such roofs where parapets are installed using Base Tie In method.
4 – IDIOTS with expensive roofing equipment: I already touch on this topic in #1, but will say this again – while you will find these “endangered species” in the wild, they are far and few between, as most of them don’t have the fund to invest, and stick with rubber.
Most common today, is to find a clown-roofer with a $100-150 hand welder from AliExpress … back 5-10 years ago, all we had was a $500 Leister Triac or the $350 “less-know-brand” (I don’t remember the name, but it was black plastic, instead of Leister’s green).
Still, you don’t often see clowns with a laser-guided $10,000 Leister Varimat V-2. Bottom line, chances of having a clown, if you are getting a residential flat roof installed, are 80% for EPDM and 30-50% for PVC / TPO … while not great, I still like the PVC/TPO odds better.
4.1 – IDIOTS in Residential Application: You see – most of our readers are homeowners, and thus, this article is geared more to residential flat roofs, while most of your experience is in commercial.
So in residential, most roofers only do shingles, yet when a homeowner ask them to do a flat roof, many will say yes, and do a hack rubber job. These homeowners will 98% of the time not ask a commercial roofer that specializes in flat roofs, to quote them, because even a non-union company will be at least 50% higher than any residential roofing contractor.
5 – TPO I’m not sure where you got the idea that I like TPO. In fact, I don’t. I’m a true PVC fan, and consider TPO to be vastly inferior! I can go on and on about manufacturers putting in cheap fillers into TPO sheet, to build up the thickness, and changing formulation all the time, without any accountability, or even letting the “public” know what is the current formulation. Also compatibility between early and late TPO products, cross compatibility between manufacturers, curing, cracking, seam voids, etc. However this wouldn’t be the right “forum” to discuss it. We can start a separate thread on this.
In my opinion, TPO is not much better than EPDM, because many if not most TPO systems today, still require GLUE for flashing, cover tape, etc. While most of it you can weld, for some reason, TPO manufacturers offer peel+stick+primer products for TPO … I just can’t understand why … but it seems to me that it’s because weld-in TPO flashings do not work well at all. Also, you don’t have much choice for TPO flashing… pipe boots, inside corners, and that’s about it… With PVC, selection of flashing is much wider, to fit job-specific requirements.
That’s why I always say “PVC / TPO”, where I put PVC first. Only when it comes to TPO vs EPDM, will I say that TPO is better.
However, as you mentioned Firestone and most other commercial roofing manufacturers, pushing TPO really hard in the past decade, made TPO “popular” among contractors, and made it “known” to building owners / architects / specifiers, and to lesser degree, homeowners.
The good thing for homeowners, is the fact that most if not all TPO products do not have residential warranty.
BTW, I would like to discuss failed TPO roofs with you … perhaps over email. Let me know if you are open to it.
5 – REPAIRS Repairs on EPDM – you often run into situations, where multiple repairs were done already … say it’s a corner of roof hatch or chimney … First corner was done with 6″ flashing… then 9″ was added on (you are lucky if they used 12″ instead of 9″) … and now what do you do? You have to tear all that flashing off, because adding more to the pile, won’t really work. And when you try to tear it off, you pull the rubber off insulation… and now it’s flapping in the air … not pretty, and very hard to get it watertight.
TPO – you and I agree that many times older roofs are hard to weld to.
PVC – most if not all products, regardless of age or manufacturer, are compatible, and far easier to repair that EPDM.
6 – COST I did a thorough analysis between TPO and PVC prices and PVC, while more expensive per square foot of material, will actually cost SAME or LESS than TPO, when you calculate total system cost (membrane, flashing, metal, etc).
Rubber will be 15% less expensive than TPO for materials only. However that 15% in material costs should only be 5-8% in installed cost difference – right?!
Still, most quotes for PVC and TPO will be 30-40% higher than Rubber, while installation is equally time consuming.
I honestly don’t know how roofers come up with these numbers, but for me, when I quoted PVC, I was higher than TPO and rubber, to separate us from competition, and build in VALUE or PREMIUM effect, that comes from attention to details during installation. And we actually did provide this extra value, by not cutting corners.
And as it relates to other roofers – I think they are doing the same PREMIUM product thing, but many don’t provide premium service.
7 – DO YOUR RESEARCH Yes, building and home owners should do their own research, but not just about materials. Installation is arguably more important, and the unfortunate truth for residential flat roof market, is that most installers are utterly incompetent. Chances of getting a better roofer are much higher, if homeowner hires a roofer that will do PVC or TPO. That doesn’t guarantee quality… but merely increases the chance by 50% 🙂
I recently came across a comment by homeowner – in a nutshell, they had a proposal to install TPO directly over asphalt shingles. I hope I don’t need to go further…
As for your statement that “this has not been good information” – again you are looking at it from a commercial roofing point of view, whereas most of our readers are homeowners with a flat roof, that have had enough nonsense with rubber and BUR, and what I’m trying to do, is help them avoid hack roofers / idiots / clowns with a “paint brush & seam roller” that do it all, since this problem is much more wide-spread in residential market.
Thanks for the great information.!
I am a career roofer, in the harsh climate of northern WI. Appx 90% of the roofing i have done has been flat work, probally 50% epdm, 25% tpo & pvc, and 25% BUR. From my experience, ifioffendyou is an experienced roofer, with great knowledge of the commercial roofing trade. From his comments, i have no doubt that he has spent a tremendous amount of time working on flat roof’s. I have seen many epdm rooofs fail in 5-7 years, and almost every single one has some of the same install error’s. Not being terminated at angle changes, lack of water cutoff, corners done incorrectly, pic on this page of seam being done, another classic rookie mistake. They did not use any wood block on the permeiter, and ran substrate right to the egde. Should have used strips of plywood ripped to 3.5″ in this case as a nailer for the egde metal. Epdm roofs can be installed correctly, with seam tape, and last along time, whether a ballast system, fully adhered, or mechanically fastened, however on a mechanically fastened system, reinforced epdm should always be used.
This article is horribly untrue and misleading. You blame the material for workmanship problems. You claim the seams will surely fail after 7 years. That is completely false. I agree that there are many incompetent and unscrupulous roofers botching up EPDM jobs. But the same is true for every other type of roofing as well. It has nothing to do with the material. It’s like if you brought your truck in for an oil change, and the Grease Monkey forgot to tighten the drain plug. Would you blame the oil when it leaked out?
It is now and undisputable, proven fact that a well-designed, well-constructed EPDM Rubber roof will outperform almost any other roof. We are currently maintaining several ballasted EPDM roofs that are well over 30 years old, and still performing well. Every night I sleep under an EPDM Rubber roof that we installed on my own home 27 years ago. And it looks like it will last many many more years. If anybody doesn’t believe that, send me an email. I will invite you to come and inspect it.
Joel,
I don’t know what state you are in, but in most states now, roofers can only use Low VOC primer, which barely holds the seams together (and costs ridiculous amount). But even if we consider the old “high” voc primer, seams still come apart, when you have even a little ponding water, and freeze/thaw/freeze action.
It’s completely natural for glue (primer) to break down with time, and water, as well as many other factors speed up that process.
“It is now and undisputable, proven fact that a well-designed, well-constructed EPDM Rubber roof will outperform almost any other roof.”
What does it even mean “outperform”? What are your criteria for that? And who “proved” this and made it a fact?
Almost every EPDM roof 10-15 years old, needs resuming, because glue/primer bonded seams begin to leak. The cost of reseaming is about $12-20 / linear foot. You can be looking ate several thousands in maintenance/repair costs on a 30 square roof, just to apply cover tape over leaking seams.
Now compare that to “almost any other roof” such as PVC / TPO, where you probe the seams, find voids, re-weld or patch. THe whole repair can be done for less than $1000.
We’ve fixed a huge PVC roof in Boston on a 20-story apartment building, with over 100 penetrations (idiots were breaking ice with sharp steel rods), and the whole job was like $2000, done in one day by 2 guys. You cannot do that with rubber.
And i’m not even talking about EPDM shrinkage issues, which other materials do not have.
I mean – you love rubber, great. I’m a PVC guy. I’m sure you do good job, and your roofs last longer than average. But average for EPDM is pretty low…
Good luck
I have a medium size roofing company that does about 3 to 4 million in sales a year. I would highly recommend either fully bonded EPDM or fully bonded TPO roof systems. I do not recommend PVC simple because I love and respect my employees. When welding PVC seams, workers are exposed to cancer causing fumes. How could I live with the fact that I had cause someone to die from such a horrible disease. By the way, in our area there are plenty of Cowboys installing PVC and TPO roofs and making a real mess of them.
As for EPDM creeping and pulling on parapets, this will never happen on a properly installed fully bonded roof.
The best way to ensure a properly specified and installed roof is to hire a manufacturer accredited roofing company and make sure they have employees not Subcontractors.
I call your EPDM assessment acurate only when the material is in the hands of an amateur.
The same is true of any roof system.
I have sucessfully installed tens of thousands of squares in EPDM.
EPDM in the hands of a trained and responsible installer is one of the very best roofing systems.
All types of roofing systems should be specified and installed by trained professionals.
The building owner/manager should always make sure they are dealing with a certified installer and that the manufacturer has approved the specifications and will inspect the job prior to release of the warranty.
Tom,
Have you aver seen TPO/PVC shrink to the point of ripping out edge metal or a brick parapet wall? I haven’t and am 99.999% sure, that you haven’t seen one either.
On the other hand, EPDM does this all the time, after 10-15 years. And it has nothing to do with amateurs installing it.
I agree that any great system can be botched up by an idiot, and a crappy roof that’s well installed, can last 3 times longer than it should. There are many factors that come into play.
With that said – EPDM is the only system for flat roofs (I don’t consider self-adhered mod-bit such as Flintastic and Libery to be flat roofing products) that amateurs and idiots have easy access to – that is why there are so many horrific EPDM installs out there.
How would a homeowner know if roofer is an idiot or a pro (when it comes to flat roofs)? These guys don’t have “IDIOT” stamped across their contractor license, and they may have stellar references from their shingle clients…
You see – to get into Thermoplastic (TPO/PVC), roofers would need to at least buy 1 decent heat welder ($500+) but usually 2-4 per crew. And for bigger jobs, a Varimat robotic welder ($10000 + generator + cords) … so an investment of $2K to over $12K is needed. This keeps most idiots out of PVC/TPO.
With EPDM, alls you need is a paint brush – and you are a “commercial roofer” 🙂 So in my opinion, EPDM is bad for homeowners on so many levels, that it’s not worth the risk.
This is not to say that there are no good EPDM roofers… it’s to say, there are too many idiots to take the risk.
When I started doing PVC 13 years ago, my I immediately spent $1000 on two Leister hand welders, and on our first big job we bought a Varimat (a measly $6K at the time) …. We were in for a long haul, and did recoup our investment many times over … but we specialized in a niche and stuck with it. Roofer with a paint brush – screw one job… move on to next …